Embraer Files Patent for New Control Surfaces
In a patent filing published in January, Embraer has revealed possible plans to incorporate entirely new control surfaces in their future aircraft designs. Described as “longitudinal control augmentation surfaces,” they resemble elevators and are shown in patent images to be affixed to the engine pylon trailing edges of the company’s proposed Energia alternative-fuel concept aircraft.
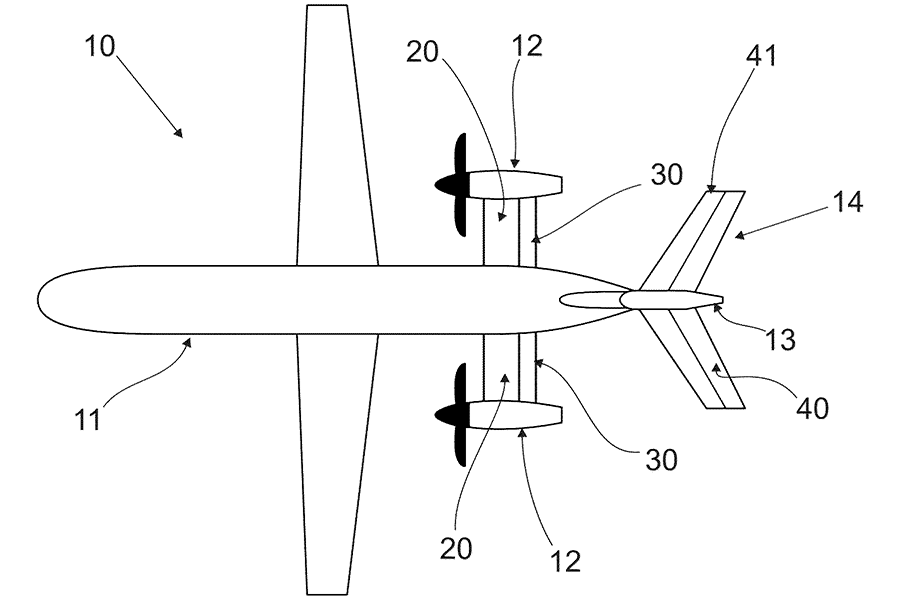
Touted as the next generation of sustainable, low-emission aircraft, Embraer presented the Energia concepts in 2021. Encompassing hybrid-electric, full-electric, hydrogen-electric, and hydrogen/SAF power plants, the proposed family of aircraft ranges in size from 9-50 seats. Three of the four concepts incorporate twin power plants mounted on pylons at the aft end of the fuselage. Technical details were sparse, however, with no mention of any new or advanced control surfaces
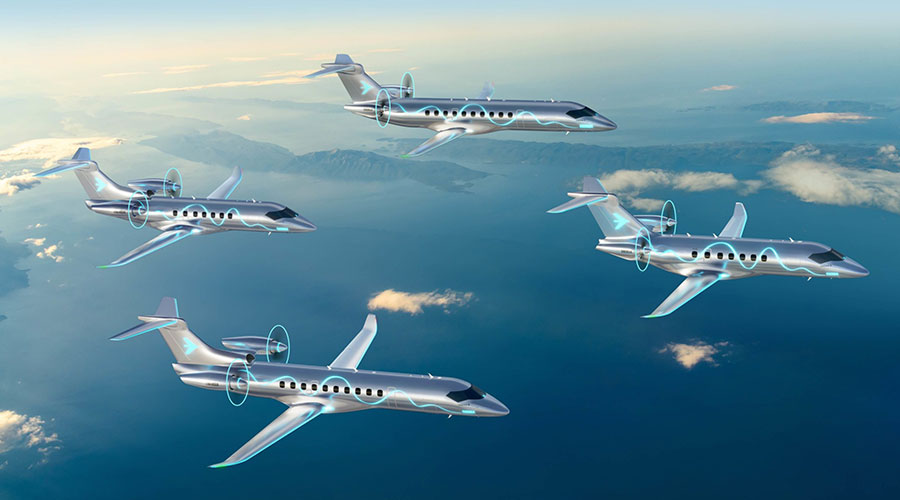
The new control surfaces described in the patent would supplement the traditional horizontal stabilizer and elevators, augmenting pitch control as well as reducing trim drag during various phases of flight. The patent, filed in September 2023 and published on January 11, 2024, is currently pending. An earlier World Intellectual Property Organization (WIPO) version of the patent application was published in September of 2022.
While the concept is a first for Embraer, the idea of pitch control surfaces affixed to engine pylons is not new. It is, however, extremely rare, as only one modern production aircraft – the McDonnell Douglas MD-90 – has ever employed the concept.
Designed as a modernized replacement for the MD-80 series, the MD-90 incorporated larger, higher-bypass turbofan engines in place of the legacy JT8D engines. The new engines were notably heavier than those it was replacing, adding a total of 1,960 pounds to the aft end of the aircraft. During testing, McDonnell-Douglas discovered the jet could, in certain flight regimes such as deep stalls, lack sufficient nose-down authority due to the added weight.
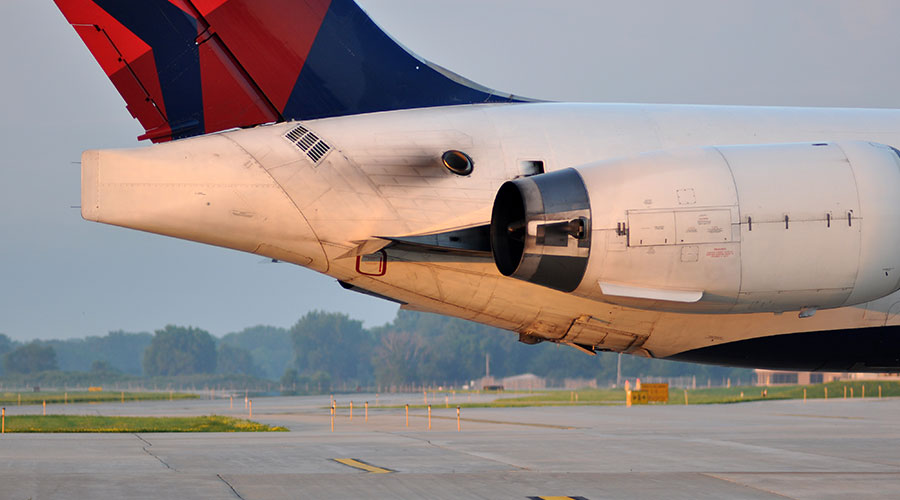
To improve nose-down authority, engineers designed what the company called “pylon flaps” – hydraulically-powered control surfaces that deploy when the control yoke is pushed near full forward position. These deflected downward only as an aid to reduce the aircraft’s deck angle and angle of attack.
When analyzing the new Energia concepts, Embraer identified the potential to employ similar control surfaces as a method to improve pitch authority as well as to reduce drag. Because the propellers employed in the concept aircraft are of such a large diameter, they necessitate correspondingly long engine pylons to provide sufficient clearance between the propeller tips and the surface of the fuselage. To ensure engine pylon rigidity, the pylons themselves must incorporate a sufficient chord, or longitudinal thickness. This combination of a large chord and long pylons creates significant surface area at the extreme aft end of the fuselage, which acts as the feathers of an arrow, naturally resisting any change in pitch.
The easy and precise adjustment of an aircraft’s pitch is a desirable handling characteristic. When analyzing the effect of the large engine pylons, Embraer determined that they would introduce so much longitudinal (pitch) stability, they would inhibit this quality. Accordingly, Embraer’s pylon flaps are designed to deflect both upward and downward in concert with the traditional elevator to counteract this stability effect and add additional pitch authority.
This additional pitch authority is obviously beneficial to aircraft control, but Embraer also presents it as a means of drag reduction. The company reasons that due to the increased stability created by the large engine pylons, using elevators alone would necessitate large elevator deflections. This, of course, would generate a correspondingly large amount of drag. By supplementing the elevators’ pitch authority with that of the pylon flaps, each control surface would deflect to a lesser degree to achieve the same effect with less drag.
The patent acknowledges the potential of canards – small wings mounted to the forward section of the fuselage – to achieve the same result. While this alternative would provide some benefits, such as a longer moment arm and light structure, Embraer observes that canards would present compatibility issues with jet bridges and ground support equipment. Additionally, de-ice/anti-ice systems would have to be duplicated for these forward airfoils, introducing additional weight and complexity.
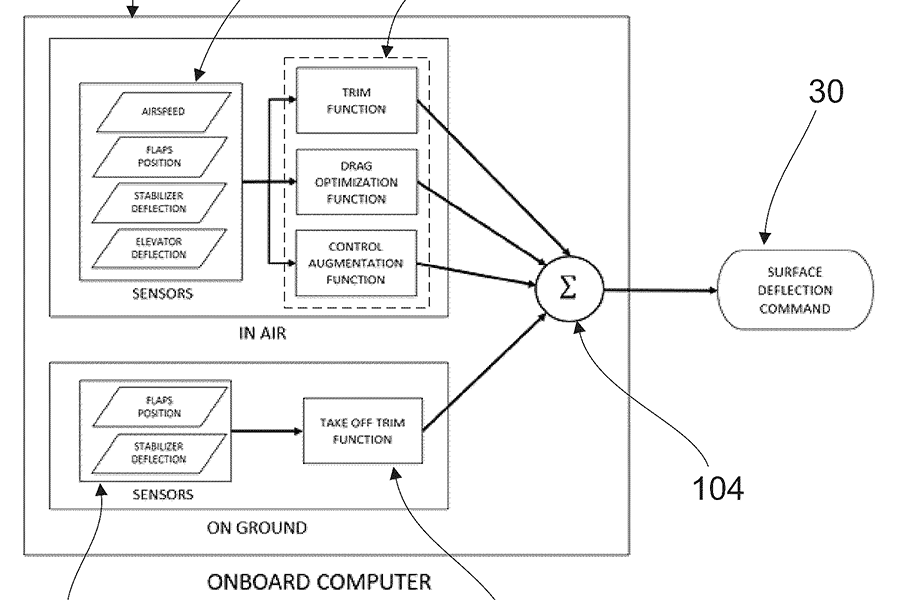
By acting in conjunction with the traditional elevators, Embraer’s patent application proposes that the pylon flaps will also trim and balance the aircraft, continuously distributing the forces and moments that change throughout the aircraft’s flight envelope. For example, as the aircraft’s flaps deploy and alter the local airflow around the engines and engine pylons, the pylon flaps can deflect accordingly to accommodate this altered airflow, ultimately reducing drag. In a manner similar to gust-alleviation systems that actively react to and counteract the effects of turbulence, these active pylon flaps are described as continuously reacting to local airflow to reduce drag.
Because of the complexity of the local airflow that envelopes the fuselage, wing, engine pylons, and tail section, Embraer specifies that the pylon flaps would be capable of deflecting in a different direction than the elevator. The extension of flaps, for example, might require an elevator input in one direction for controllability but a pylon flap deflection in the other direction to reduce drag. There is no indication in the patent description that the pylon flaps will be able to be independently controlled by the pilots, implying the pylon flap activation and control will be fully autonomous.
Finally, Embraer describes how the pylon flaps can increase the propulsive efficiency of the powerplants and propellers. By altering the shape of the pylon upon which they’re mounted, the ensuing changes in pressure and drag could increase the effectiveness of thrust production. This would have the secondary effect of enabling a slightly lower power setting for a given segment of flight, reducing fuel burn and increasing operating efficiency.
While the introduction of this new technology is far from certain and years away at best, the patent application signals Embraer’s continued investment in and dedication to the advanced concepts they’ve been showcasing in recent years. It also is an indication that Embraer is taking a holistic approach to its next-generation aircraft, incorporating an array of emerging technologies as opposed to updating existing platforms with next-generation power plants.
Topics Related To: FUTURE OF FLIGHT
Skyryse – Simplifying Aircraft Control with New Technology
Aviation startup Skyryse progresses toward FAA certification for a revolutionary new pilot/aircraft control interface that can simplify piloting and increase safety.
Flaris LAR-01 Very Light Jet Progresses Toward Certification
The Polish Flaris LAR 01 very light jet continues its progress toward certification and production.
Light Aircraft Manufacturer CubCrafters Tests Electric Lift Augmentation to Enable Slower Flight for Short Field Operations
Through the use of ducted fans mounted on the wing, light aircraft manufacturer CubCrafters tests electric lift augmentation to boost slow flight and short-field performance.